Eight years ago, Justin Vandevoort was working in a glass factory when he applied for a much more advanced job at MRG Tool & Die in Faribault, Minn.
Look to apprenticeships to jump into hot jobs like skilled manufacturing
Thanks to the tight workforce and more state investment, employers statewide are offering on-the-job training for hard-to-fill jobs.
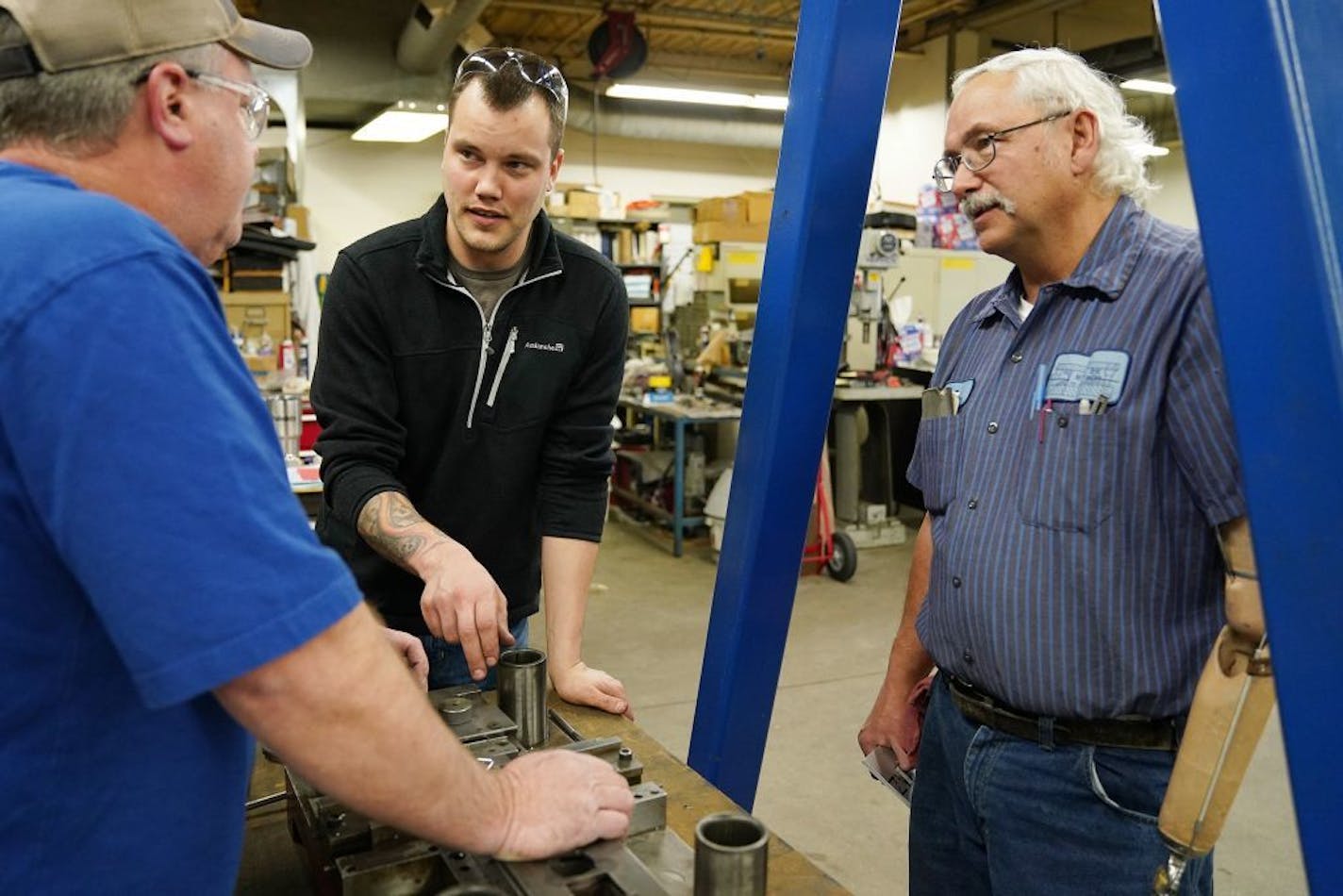
"My interview was like 'The Gong Show,' " the 31-year-old said. The interviewer asked if he knew how to use different types of machines, and he continually said no but he was willing to learn.
Yet Vandevoort was persistent. "I kept calling back and bugging them," he said.
That hustle impressed MRG President Rod Gramse and won Vandevoort not only the job, but three consecutive MRG training programs that gave him the skills to run the company's waterjet cutter and the thundering punch presses that make high-precision industrial parts for autos, planes, medical devices and agricultural equipment.
Last month, he graduated from MRG's 10-month leadership apprenticeship program and was named MRG's new pressman leader. He's replacing supervisor Ben Froman, who is retiring after 25 years.
Vandevoort is one of Minnesota's 2,242 workers who gained industry credentials and new skills with the help of $5,000 state apprenticeship or training grants offered to employers in manufacturing, information technology, health care and agriculture.
Driving the change is not only more state investment but also employers' needs to replace aging workers at a time when unemployment has been at historic lows.
The programs are desperately needed as Minnesota employers struggle to fill 75,400 jobs amid soaring baby boomer retirements and a swelling skills gap, said Jacqueline Buck, employer services director at the Minnesota Department of Employment and Economic Development (DEED).
For those who are seeking skilled manufacturing and other jobs that need extra training — which employers across the state say are going unfilled because of lack of qualified workers — there are several avenues to tap into apprenticeship opportunities.
Training programs often last one to three years and can cost $15,000 to $20,000 per person. However, training costs are often covered at least partly by employers or unions. Job seekers need to ask.
Most of the industrial trainees in the state are beneficiaries of grant programs administered by DEED, particularly the Pipeline and Minnesota Apprenticeship Initiative programs.
The state grants and training like the ones Vandevoort used let workers earn a paycheck while they learn the job. The idea is that workers get regular pay increases as they pass a skill set or meet classroom hour goals, Buck said.
Interested job seekers can get help at one of Minnesota's 50 Career Force Centers or online at MinnesotaWorks.net, ApprenticeshipMN.com, MnCareerPathways.org and dli.mn.gov/pipeline. The websites give step-by-step directions to finding employer job lists, industry-certified apprenticeship programs and company training.
Buck suggests that job seekers contact companies directly to learn if they still have trainee slots.
MRG, which hired and trained 13 inexperienced workers in five years, joined the Minnesota Apprenticeship Initiative program two years ago and now gets a $5,000 grant to help defray the cost of training that can reach $15,000 per apprentice, Gramse said.
MRG, which hired an outside firm to run in-house training, has two apprenticeships. One teaches management skills. The other trained workers like Derrik Richardson to operate machining robots that mill chunky metal blocks into auto and airplane parts.
Nearby in Faribault, companies such as Sage Electrochromics, Daikin Americas and Saint-Gobain took a different approach, using Pipeline grants from Minnesota Department of Labor and Industry and community colleges to train workers in skills such as welding, electrical work and machining.
Buck said the chronic labor shortage has propelled the state and employers to do more to showcase its training grants and partnership programs. Last year's stepped-up outreach really helped hiring numbers.
As of last year, Metro Transit's apprenticeship program attracted and trained 200 Minnesotans to become certified bus drivers. It's looking to hire more apprentices as a way to address a severe driver shortage, Buck said.
Viracon in Owatonna, Minn., which made the building glass for U.S. Bank Stadium and the One World Trade Center, hired four apprentices and is looking for two more.
Owens Corning in Minneapolis, Spectro Alloys Corp. in Rosemount and Aero Design and Manufacturing in Duluth also hired apprentices for multiyear training.
Company trainees and state-sponsored apprenticeships enrolled in formal certified programs usually get a mix of on-the-job learning and classroom instruction that lasts 12 to 36 months. They give workers industry-recognized credentials along with raises, career direction and newfound loyalty, Buck said. They can also help employers address production backlogs and speed up growth.
MRG generates roughly $10 million in revenue and is growing about 3% a year. It could grow faster — "I have more machines than I have the people to operate them," Gramse said. "The limitation is finding the right skilled people to keep the machines set up and running."
Annie Welch, who runs the state's Dual Training Pipeline Grant Program, said the state is rolling out more grants to help employers get more workers in the door.
Last June, Minnesota's Department of Labor and Industry awarded 60 employers new "Pipeline" job-training grants worth $2.9 million. The funds allowed another 664 workers and new hires to get paid while working, training and taking college classes in the fields of manufacturing, health care, IT and agriculture.
Unlike certified apprenticeships that end with workers having industry-recognized degrees and certifications, the Pipeline grants help employers provide on-the-job training needed to advance careers inside factory or health care or IT settings.
With the newest round of grants, the number of Pipeline trainees grew to 1,350 since the program's creation in 2015.
Participating Pipeline employers include Standard Iron and Wire Works in Monticello, Alliance Machine in Elk River, Iron River Construction in Chaska, Jones Metal in Mankato, Standard Iron and Wire Works in Monticello and Yeager Machine in Norwood Young America.
Dee DePass • 612-673-7725
Pioneering surgeon has run afoul of Fairview Health Services, though, which suspended his hospital privileges amid an investigation of his patient care.