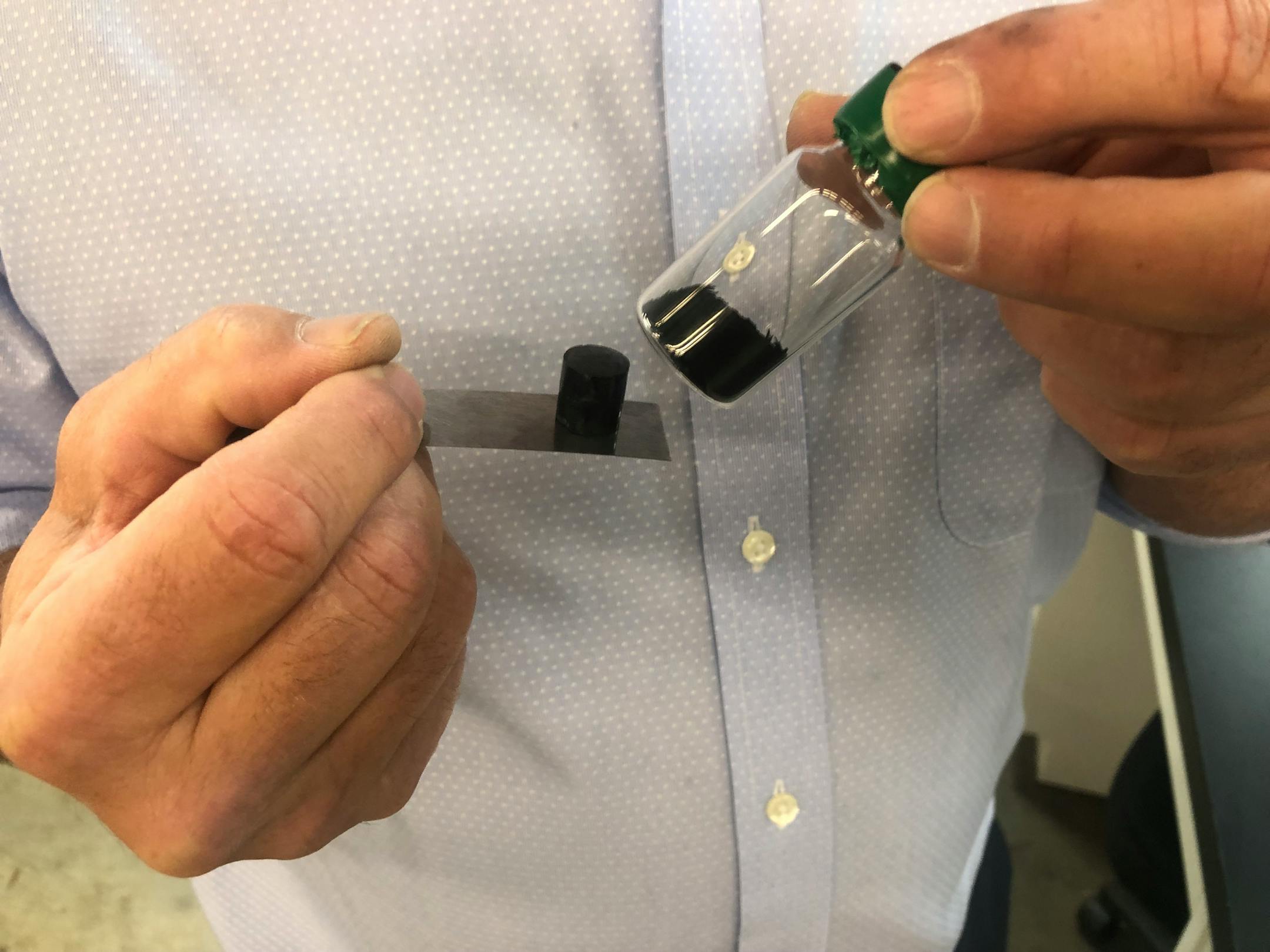
Niron Magnetics of northeast Minneapolis is commencing production of next-generation electric-motor magnets to power a greener economy with global industrial partners.
Niron has built a 22,000-square-foot site to produce prototype magnets from lower-cost, domestic materials, including iron or recycled steel and ammonia.
They will be used in wind turbines, electric vehicles and other electric motor-powered equipment that today are largely reliant on increasingly expensive magnets made from rare-earth materials mined in China.
"There was lots of scientific and engineering work over the last decade," said CEO Andy Blackburn. "And now we're scaling to production. We are a 10-year 'overnight success.'''
Last week, Niron was awarded $17.5 million by the U.S. Energy Department's Advance Research Projects Agency, on top of $60 million raised previously, including $45 million in private equity.
The department has followed Niron since 2012, when its process was developed by U of M Prof. Jian Ping-Wang, a Niron founder and adviser.
"This is a precursor to full-scale production … thousands of tons of magnets for our industrial partners for electric motors in wind turbines, cars and other equipment that requires an electric motor,'' Blackburn said.
Niron aims to double employment to 60 technicians and others and expand the pilot plant by 60% in the next year.