For years, the global supply chain was treated like a stagehand in a theater — absolutely essential for a smooth performance but hidden from the audience.
Toilet paper is back on shelves: Are supply chains back to normal?
Empty shelves in Minnesota are mostly a pandemic memory, but some disruptions are expected to continue.
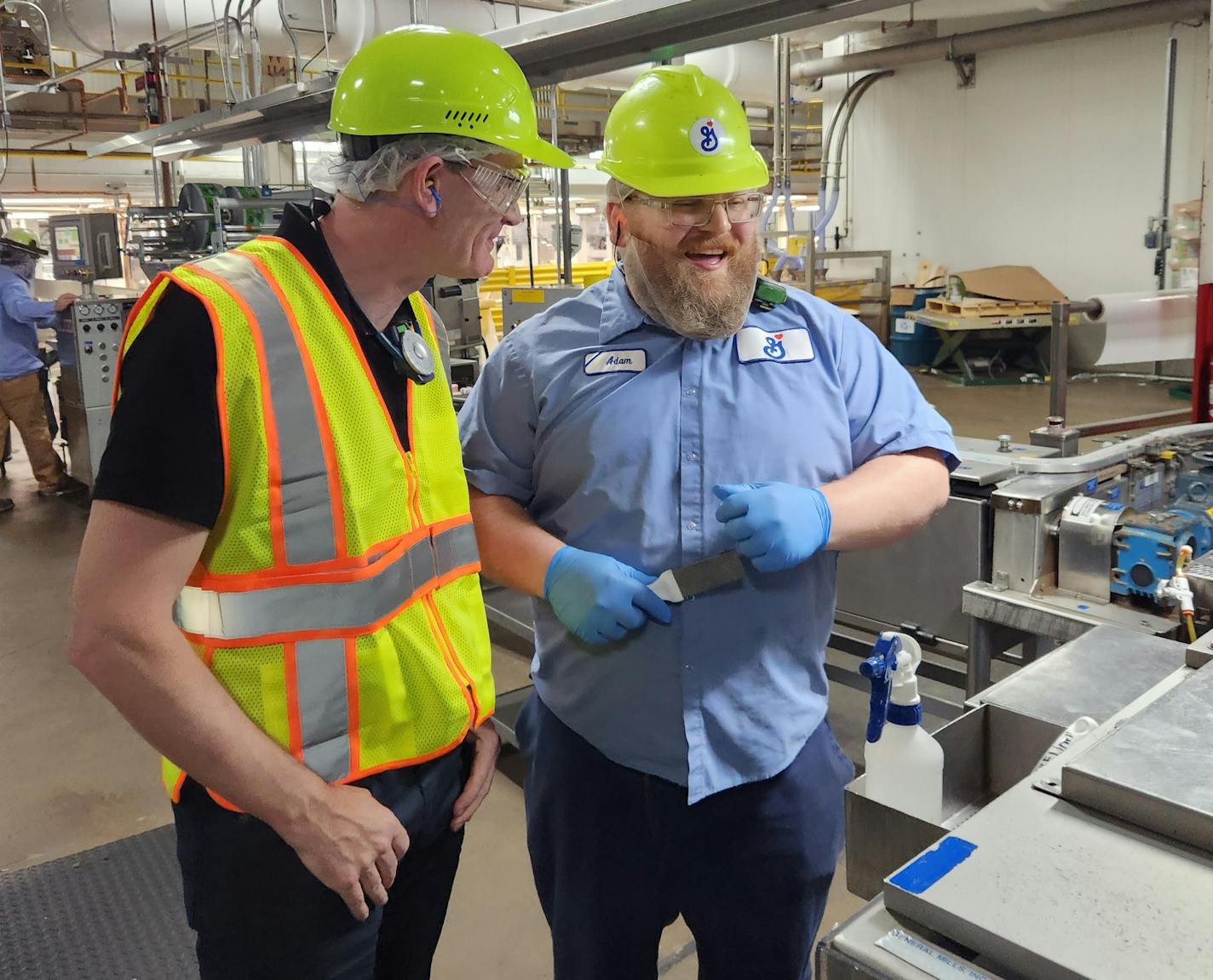
Then the pandemic thrust the term into the limelight as we faced shortages of toilet paper, cereal and computer chips. Suddenly "supply chain" was a catchall for the strange economic environment of empty shelves in a nation accustomed to surplus.
Those days are behind us as shortages are less common and the global network of makers and movers again fades into the background of public discourse. But the job of sourcing and transporting goods should now be everyone's business.
"There has been a fundamental shift in how we work," said Paul Gallagher, chief supply-chain officer at General Mills. "To get back to the calmness we want to see in the supply chain, we've got to look like a serene swan, paddling madly underwater."
At Golden Valley-based General Mills and other companies, supply-chain work is no longer relegated to a silo — and it has become much more efficient with the help of artificial intelligence.
"There's more of an appreciation of supply chain and how integral it is to delivering what our customers and consumers need," Gallagher said.
That approach helps the suppliers, manufacturers, freight companies and retailers up and down the supply chain transform raw materials into finished goods and sales in a way that meets consumer expectations — quickly and at as little cost as possible.
"Things are sort of in a return-to-normal stage, but the disruptions are going to continue," said Emily LeVasseur, managing director and supply-chain expert at Waypost Advisors in Eden Prairie. "They were always there but for some reason never really captured our attention as much."
What caused supply-chain issues to begin with?
As pandemic shutdowns took hold in early 2020, a major shift in what we buy and how caused economic upheaval, particularly because so many manufacturing, transportation and retail employees were staying home as the virus spread.
There was too much sudden demand for groceries and home goods and not enough supply — of labor, materials, trucks and rail cars — which led to shortages on shelves and contributed to inflation.
For General Mills, the supply-chain crisis meant products weren't getting to market because they couldn't be made fast enough due to ingredient shortages. At one point just 75% of orders for pizza rolls and refrigerated dough were being filled, down from a more typical 95%.
"The pandemic was a very unnerving time for a lot of people as we tried to navigate disruptions," Gallagher said. "There are still disruptions out there, but we are navigating them with more grace than supply chains would have done in the past."
What do things look like now?
Compared to the pandemic years of too much stuff selling and not enough trucks or drivers to ship it all, the supply chain now has the opposite problem — too much slack in the system.
That's great for consumers and other parts of the supply chain but tough for transportation companies as shipping costs plummet. Profits at Eden Prairie-based logistics company C.H. Robinson dropped 64% in its most recent quarter compared to the same period a year ago.
C.H. Robinson CEO Dave Bozeman told analysts last week there is "ample carrier capacity" and a key metric — load-to-truck ratio — is back to its 2019 level.
"We're building ourselves up … for the eventual rebound of the market," Bozeman said, but the company is looking for increased productivity and efficiency rather than adding more employees.
That is the case up and down the supply chain as carriers and manufacturers deal with high costs and limited labor availability, LeVasseur said.
"There is a focus on cost optimization because borrowing money is so expensive right now," she said. "Companies are trying to find ways to optimize inventory levels and add improved planning systems."
So, how have things improved?
Demand has fallen as consumers are no longer stockpiling food and other essentials, taking pressure off global logistics networks that were once visibly backed up near ports.
"We're not as focused on the tyranny of the urgent," Gallagher said.
At the same time, the rise of AI is helping companies deal with disruptions and make decisions much faster.
General Mills processes 3,000 orders a day, Gallagher said, and artificial intelligence scans for the most cost-effective ways to move those goods.
"At the moment, over 70 percent of recommendations are automatically deployed," Gallagher said, while the rest are reviewed by the company's employees in India. "That translates into time saved."
Broader understanding of supply chains — due in part to the toilet paper shortage of 2020 — has also meant better planning across departments.
"We've switched from a culture of knowing to a culture of learning," Gallagher said.
Should we expect another supply-chain disaster?
Whether supply chains have been strengthened to withstand another event like the COVID-19 pandemic is unclear. But one of the factors that prompted a shortage of materials — "just in time" manufacturing — has less prominence now.
Businesses need to find the right balance between having enough product or material on hand to fill all orders vs. having too much money tied up in unsold inventory, LeVasseur said. That balance has shifted toward more inventory, which puts financial pressure on businesses amid continued inflation and high interest rates.
"Everyone wants the inventory and doesn't want to miss a sale, but they are all asking the question of, 'How can we not have too much?'" she said.
Some of the big issues facing supply chains now are low water levels in the Panama Canal and the lower Mississippi River, which all influence how fast and cost-effectively goods get to market. Consolidation and bankruptcies in the trucking industry, gas prices, global conflicts and agricultural yields all affect costs and timing.
Yet, while "supply chain" invokes imagery of trucks, ships, machines and warehouses, Gallagher says it is people that make it all work.
"After spending close to 30 years in supply chain there's not much that keeps me up at night," he said. "What is critical is we keep people engaged."
President and Chief Creative Officer Joe Cecere of Little & Company worked with the brewery to relaunch the West Coast brand, including its hallmark IPA.